Będzie pan zadowolony, czyli jak testuje się komponenty do instalacji PV, żeby nie zaskoczyły klienta podczas użytkowania
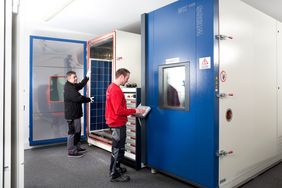
Pęknięcie szyby, hotspoty czy tzw. ślimacze ścieżki – według raportu prestiżowego instytutu TÜV Rheinland to tylko trzy z dziesięciu najpoważniejszych awarii, na jakie narażone są systemy PV instalowane z wykorzystaniem modułów niskiej jakości. Tego rodzaju uszkodzeń często nie da się naprawić inaczej, niż wymieniając cały panel, a niewykryte w porę prowadzą do przyspieszonej degradacji i niższych uzysków. Dlatego przy wyborze komponentów PV sprawdza się stara zasada: lepiej zapobiegać, niż leczyć.
Ale jak zapobiegać, jeśli wielu wad fabrycznych instalacji fotowoltaicznej nie da się dostrzec gołym okiem? Najlepiej zdać się na opinię ekspertów, którzy badaniem i certyfikowaniem komponentów PV zajmują się na co dzień. To m.in. takie organizacje, jak amerykański NABCEP czy instytuty europejskie: VDE, Instytut Fraunhofera oraz wspomniany wyżej TÜV Rheinland. To tam renomowani producenci, którym zależy na potwierdzeniu jakości oferowanych produktów, poddają swoje komponenty wnikliwej analizie.
Ci najlepsi idą jeszcze o krok dalej. Przykładowo IBC SOLAR, wiodący dostawca kompleksowych rozwiązań w zakresie energii słonecznej, oprócz certyfikowania modułów oraz konstrukcji montażowych w renomowanych instytucjach przeprowadza także dodatkowe testy jakości. Współpracujemy w tym zakresie z laboratorium fotowoltaicznym SUNLAB. To niezależna jednostka badawcza, w której prowadzone są wieloetapowe rygorystyczne testy jakości z wykorzystaniem standaryzowanych metod analitycznych – tłumaczy Maciej Drobczyk, Country Manager IBC SOLAR Polska. I dodaje: Wszystkie komponenty w naszej ofercie muszą zostać sprawdzone w SUNLAB, zanim trafią do sprzedaży. Dodatkowo moduły własne naszej marki testujemy w połączeniu z konstrukcjami montażowymi, czyli tak, jak faktycznie będą zamontowane na dachu.
Przygniatane, podtapiane i rażone prądem
W laboratorium SUNLAB komponenty PV przechodzą prawdziwy sprawdzian survivalowy na łącznej powierzchni 250m2. W trakcie statycznego testu obciążenia mechanicznego 12 pneumatycznie sterowanych cylindrów wywiera nacisk na powierzchnię modułu równy 2400 Pa w trzech godzinnych cyklach, żeby sprawdzić jego wytrzymałość. Nacisk wywierany na panel PV jest obliczany z wykorzystaniem specjalistycznego oprogramowania zbierającego dane z czujników umieszczonych na stanowisku testowym.
W komorze klimatycznej moduły są poddawane testom odporności na działanie wilgoci. Badanie przeprowadzane jest w temperaturze 85 stopni Celsjusza i przy względnej wilgotności powietrza wynoszącej 85%. Cały cykl testów trwa 1000 godzin z regularnymi przerwami na „odpoczynek” modułu w temperaturze pokojowej. Równie ekstremalne warunki atmosferyczne panują podczas testów poziomu degradacji.
Jednym z najciekawszych sprawdzianów dla modułów PV jest pomiar elektroluminescencji i mocy paneli. W ramach tego badania produkt jest wprowadzany do ciemni, gdzie po przyłożeniu napięcia elektrycznego następuje emisja światła rejestrowana przez kamerę elektroluminescencyjną. Test ten jest w stanie wykryć nawet najdrobniejsze pęknięcia w module i ewentualne wady materiałowe, takie jak np. pęknięcia włoskowate.
Ostatni test bada stopień izolacji komponentu. Chodzi w nim o przekonanie się, czy panel PV jest szczelny i tym samym odporny na działanie czynników atmosferycznych, takich jak śnieg, deszcz czy poranna rosa. W tym celu moduł jest zanurzany w zbiorniku z roztworem wody oraz specjalistycznego środka i obliczany jest pomiar rezystancji izolacji. Choć krótkie, bo trwające zaledwie dwie minuty, to badanie jest jedną z najważniejszych metod zapewniania bezpieczeństwa elektrycznego instalacji – wyjaśnia Maciej Drobczyk, Country Manager IBC SOLAR Polska.
Huragany i burze niestraszne
W IBC SOLAR rygorystycznym standardom jakości podlegają nie tylko moduły PV, ale również konstrukcje montażowe. Firma opracowuje technologie pozwalające na tworzenie balastowych systemów montażowych, które wymagają minimum obciążenia, nie przebijają poszycia dachu, a jednocześnie zachowują najwyższą stabilność i bezpieczeństwo. By umożliwić rozwój takich produktów konieczne są testy w tunelu wiatrowym.
Jedną z organizacji, która od 30 lat przeprowadza pomiary w tunelu aerodynamicznym ze skalibrowaną warstwą graniczną jest Instytut I.F.I w Akwizgranie. Tam właśnie IBC SOLAR bada swoje aerodynamiczne systemy montażowe. Na potrzeby testów budowany jest model budynku w skali 1:50, na którym umieszcza się system fotowoltaiczny. Tak przygotowaną makietę wprowadza się do tunelu testowego, gdzie sześć wentylatorów osiowych z silnikami elektrycznymi o mocy 22 kW wytwarza wiatr. Na odcinku rozbiegowym o długości 10 m wiatr staje się turbulentny, a następnie uderza w model budynku. 360 punktów pomiarowych znajdujących się na makiecie pozwala zidentyfikować i zapisać, jak warunki wietrzne oddziałują na system PV.
Po wykonaniu testu producent otrzymuje certyfikat na przebadany system montażowy oraz narzędzie obliczeniowe, za pomocą którego można określić wpływ wiatru na instalację. W ten sposób wiadomo, w którym miejscu konstrukcja musi być obciążona balastem.
Cztery dekady doświadczenia
Na jakość, z której IBC SOLAR jest znany na całym świecie, składa się nie tylko dbałość o wysoką klasę oferowanych produktów, ale także solidne kompetencje i know-how pracowników oraz partnerów premium firmy. Obchodząca w tym roku 40-lecie istnienia marka od zawsze stawiała na rozwój umiejętności swoich specjalistów, jak i edukację branży. W tym celu 10 lat temu założono wewnętrzne centrum szkoleniowe pod nazwą IBC SOLAR Competence Center. Organizowane tam wydarzenia przeprowadzane są w formie webinariów online, warsztatów stacjonarnych, a także szkoleń w siedzibie klienta. W zależności od obszaru tematycznego szkolimy uczestników o różnym stopniu zaawansowania. Od doświadczonych partnerów premium po instalatorów, którzy dopiero rozpoczynają przygodę z branżą odnawialnych źródeł energii lub chcą zdobyć dodatkowe umiejętności i wiedzę – wymienia Maciej Drobczyk.
Jednym ze szkoleń w ramach IBC SOLAR Competence Center, cieszących się dużym zainteresowaniem w Polsce, są warsztaty z bezbalastowych konstrukcji montażowych na dachy płaskie organizowane wspólnie z CW Lundberg, producentem kompletnych systemów ochrony dachów oraz firmą Eko Projekt. Ponad 150 osób wzięło udział w dwóch edycjach tych szkoleń. Zapisy do udziału w kolejnej edycji rozpoczną się jesienią 2022 roku. Terminy najbliższych webinarów i warsztatów stacjonarnych można sprawdzić na stronie internetowej firmy.